There is a lot of hype about AI these days. But who needs hype when you want to build something impactful? You need Lean AI.
Any start-up worth its salt has been pitching it’s AI capabilities to investors in order to secure funding.
Previously these types of companies will have been lapped up by those looking to find the next tech unicorn, but nowadays investors are starting to be warier when it comes to investing in AI start-ups.
Why are investors warier about AI?
Well, several of the companies claiming to have AI capability in their products fail to understand how to truly make this technology work sustainability and consistently.
It has led to many launching before they are ready to and promising things that they cannot deliver.
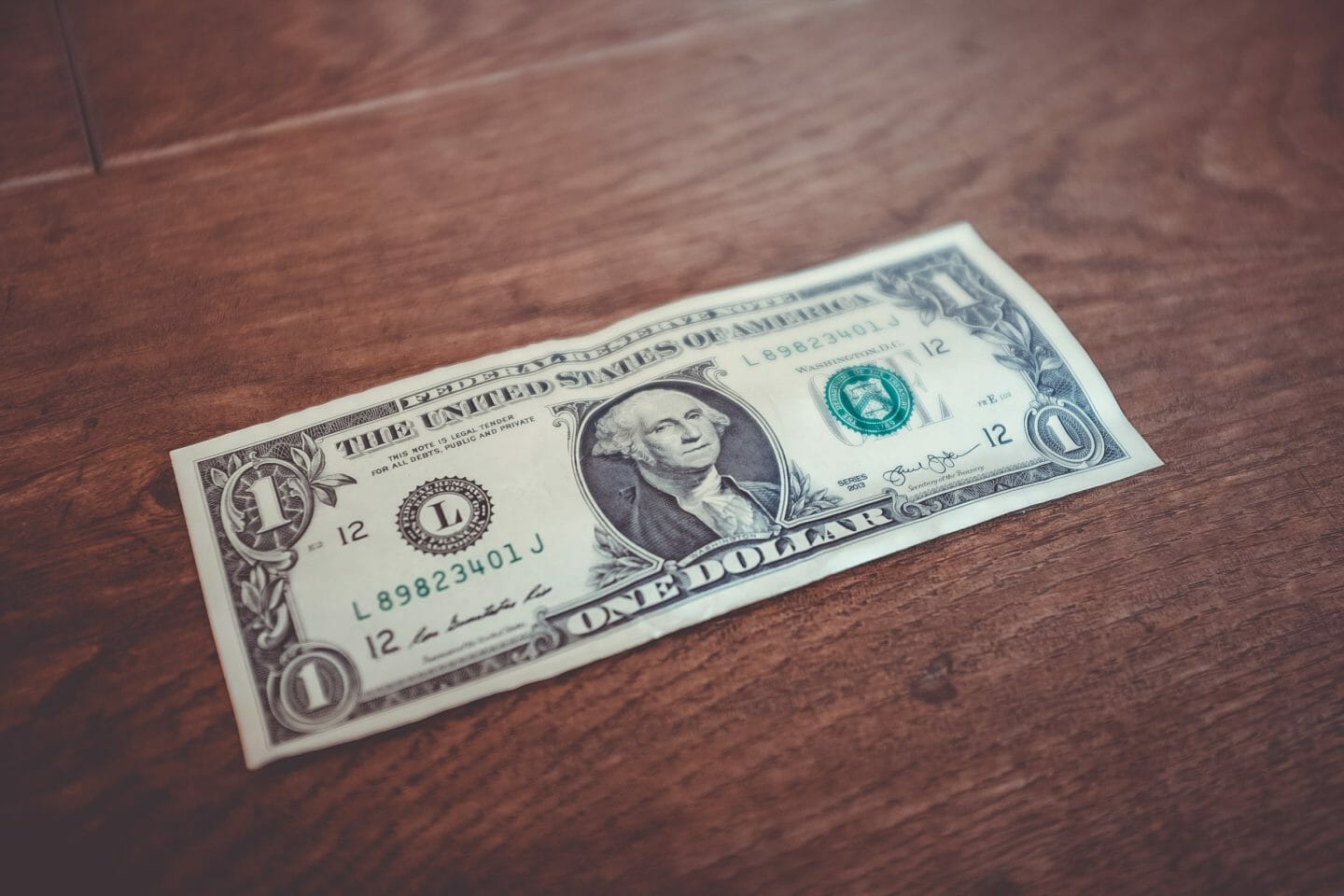
Even big companies such as Tesla have seen challenges when they have tried to roll out AI-based capabilities too soon. For example, the recent launch of Tesla’s summon technology to find your car has had trouble.
So how can companies really take advantage of the possibilities that I offer is the right way?
There are several great ways in which AI can help us build more impactful products. One of the mat the benefits of AI is allowing you to gain insight into your customers at scale. Artificial intelligence is also great for helping you to automate existing processes and procedures using machine learning.
But how do you know when your product is likely to be successful with AI?
Now it is time for companies looking to take advantage of artificial intelligence to look to other industries.
What frameworks can we take from successful scaling operations at that can be applied to the world of AI?
Perhaps one of the most successful applications of process management comes in the form of the lean principles for development and continuous improvement.
An introduction to Lean process management
I first fell in love with Lean when I was working in the research and manufacturing company. One afternoon with some of the other graduates we were told the story of Toyota’s donation of process engineers in lieu of funding to a food bank in New York.
The charity had for years reached out to big corporations to get funding to support their activities in offering services to homeless people over create the Christmas period.
One year Toyota said that instead of offering them funding and they would loan some of their process engineers to the charity.
In came the process engineers from Toyota to conduct a Kaizen.
During the Kaizen process, the engineers went through and understood every single part of the process is that we are being used to serve food and pack emergency supply boxes for customers of the food bank in New York.
Once they understood the process the engineers then worked to improve it cutting the wait time for food from 90 minutes to 18 minutes.
In addition to this, they were able to reduce the time that volunteers spent filling these food bags from 11 down to 6 minutes per bag.
The difference in how the centre is run and the impact that they were able to make on people was way more than could’ve been achieved had Toyota just delivered funding to the food bank that year.
I found this story truly inspirational and having learnt it said about implementing the principles of learning to every project I ran.
The principles of Lean Manufacturing
There are seven main principles of running a project in a Lean way.
I have listed these principles below:
- Always focus on the customer
- Understand how work really happens
- Make your processes flow smoothly
- Reduce waste and concentrate on value
- Stop defects through removing variation
- Get buy-in from the team through collaboration
- Make your efforts systematic and scientific
The most important part of the whole process is to focus on the customer. By focusing on the customer you can ensure that you are always building with that in mind and developing something that’s going to be impactful.
So what is Lean AI?
The term Lean AI was first coined by Manifold AI in 2016. They saw the benefits of creating a mental model based on the lean methodology when running a project that uses AI.
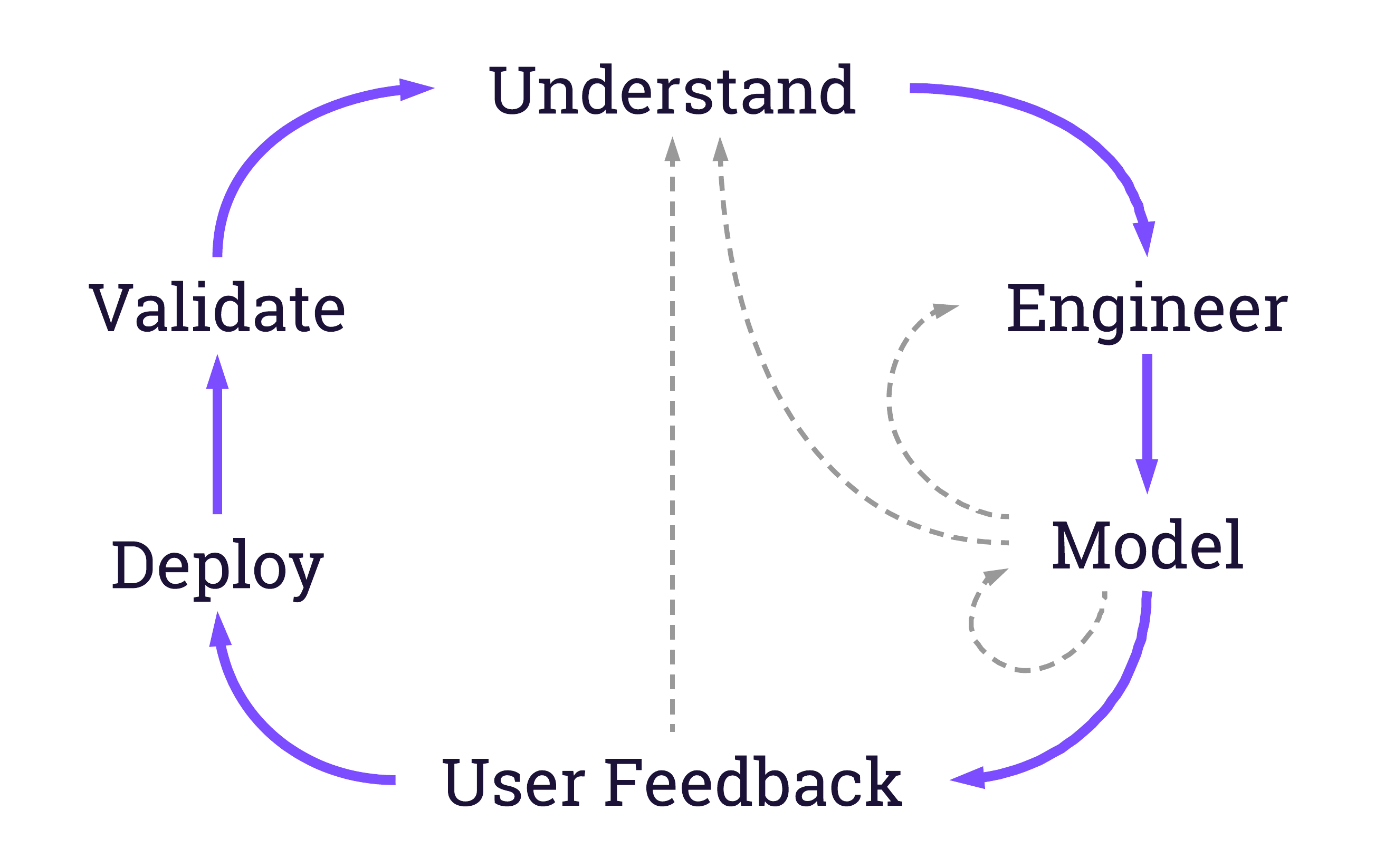
There are 6 steps involved to implement a Lean AI system:
- Problem: Understanding the problem you are trying to solve
- Framework: What is the architecture you need to support the AI product
- Baseline: Create a baseline model to understand the problem
- Feedback: Get customer feedback
- Deploy: Put the model into production
- Validate: Confirm the solution is working
By combining the customer-focused approach of lean with the scaling power of AI you’re able to develop something truly impactful.
Instead of getting caught up in the hype you can focus on the customer get to the root cause of the problem and build out a simple solution to solve it.
Once your solution is in place you can create a feedback loop with your customer to develop continuous improvements.
While many developers will be familiar with agile as a framework for development, often the customer-focused aspects of lean can be forgotten when it comes to defining the problem.
When thinking about Lean AI, I really focus on the customer and understanding the customer program problem.
Before starting any project I think about the five whys.
The ‘five whys’ is the process of asking yourself why five times when thinking about a problem root cause.
This process has been used in lean factories to identify the root cause of issues in the manufacturing process.
However, when thinking about Lean AI at Artificially Intelligent Claire, the focus is to understand the customer problem deeply before you start building out a solution.
By asking why five times you really have to understand the problem that you are trying to solve. Once you understand the problem you are in a much better position to build something that will have an impact.
Three benefits of Lean AI development
There are many benefits to building in a Lean way. Here are three that I believe are most important.
1. Simple solution
When you have a strong why it’s easier to design solutions. When you are building purely for the why of your customer problem and not ego you can:
- You can discount options quickly
- You can build stronger products
- Fit the need of the user
2. Ethical solution
When you are focussed on the why and your customer you are:
- Thinking about the end-user and the potential scenarios
- More likely to build something useful and consider bias
- Build a more ‘human’ solution
3. Impactful solution
Finally, when you truly understand the problem you are trying to solve it helps you understand which products to prioritise:
- Understand what the customer needs
- Build an impactful product
- Solve real problems
So how do you get started with Lean AI and the 5 whys?
I know you’re going to be excited to get started implementing lean AI principles into your projects.
To help you get started you can grab my guide on how to using the 5 whys to get to the root cause of Customer problems.
Enjoy!